Production Process Improvements: in order to satisfy the demands of an increasingly demanding market, you need better performance, i.e. increase current production, but how to do it? The solution is to be able to make the time available for production more efficient: working on maintenance management allows to reduce stops and, consequently, reduce production times and costs. Keeping industrial production active is the primary objective of every manufacturing company, a machine downtime, if not planned, in fact entails considerable losses in economic terms, not to mention the negative effects on the corporate image that are reflected in the relationship of trust with customers.
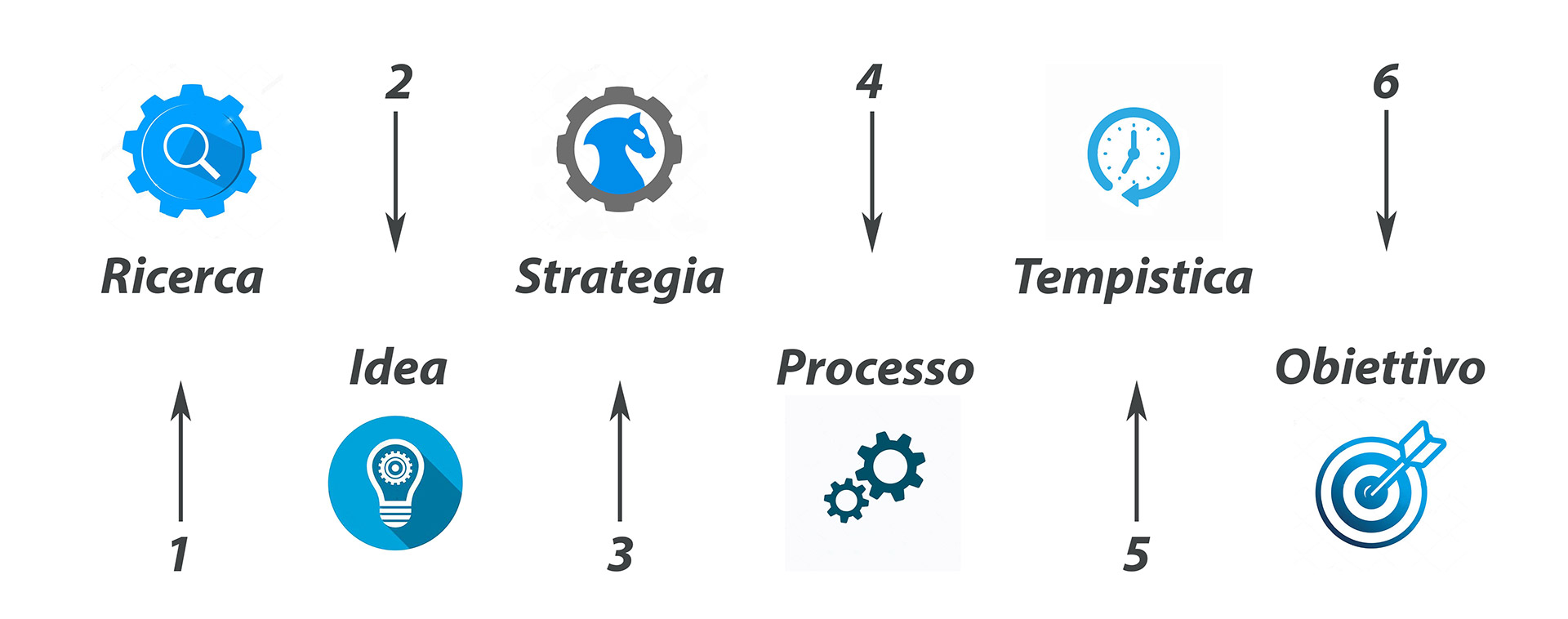
Production Process Improvements, fluid, efficient and reliable, represents an added value in any field. The production process improvement in a line or plant consist in paying attention to the 6 different production loss causes, classified as:
- Unexpected failures
- Set – up and startups
- Change formats
- No-load operation and micro-losses
- Speed reductions
- Process rejects and defects
To solve these problems and have minimum production losses, we apply different strategies and methodologies ranging from TPM to our experience that we have acquired over the years. Solutions ranging from research, to idea, to strategy, from process, to time, up to the achievement of the final goal of a fluid and dynamic production process. The purpose of this system is to increase production, reduce defects, reduce breakdowns, reduce accidents, reduce scrap and reduce maintenance costs, while keeping plants and machines efficient.
We also offer a service of reconditioning of automatic packaging machines (revamping)